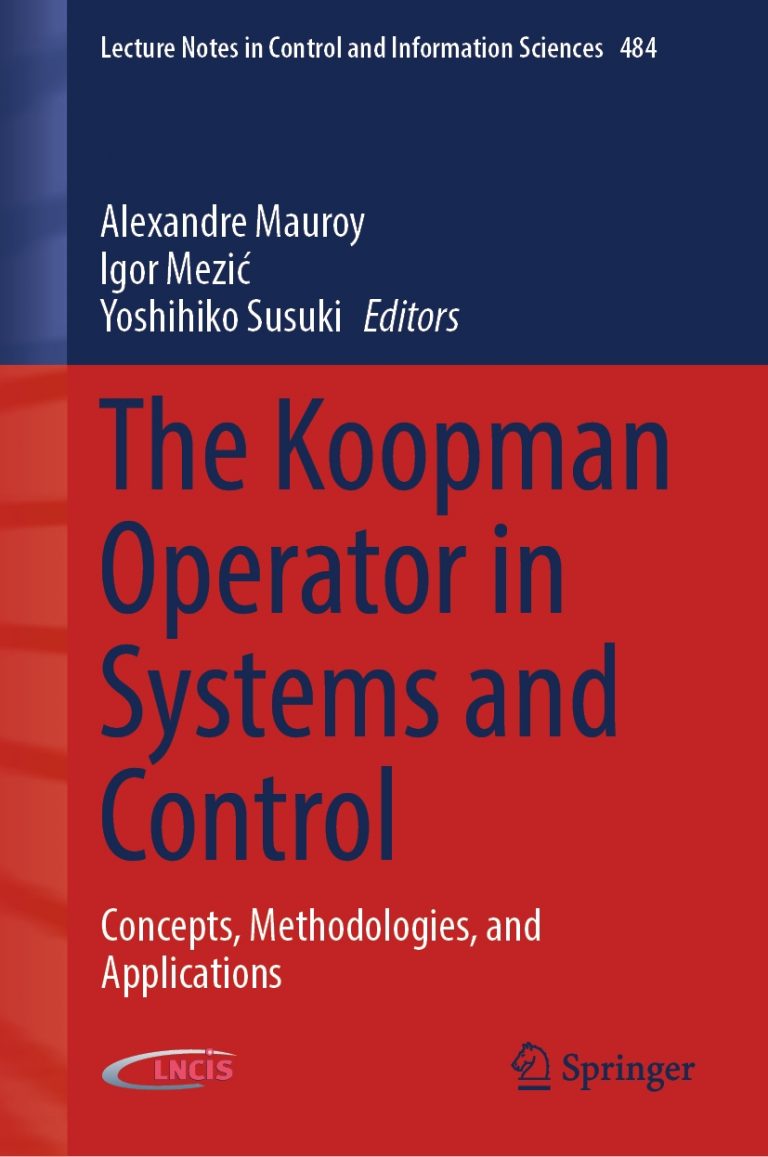
Ultra-high precision positioning devices are of outmost importance in microsystems’ technologies and precision engineering. The frictional disturbances of mechanical elements in relative motion often limit their positioning performances. If nanometric positioning precision and accuracy are aimed for, frictional disturbances have thus to be identified, modeled and compensated for via appropriate control algorithms. Suitable experimental set-ups are therefore employed to study the effects of frictional disturbances. The parameters related to state-of-the-art friction models are experimentally identified. Different control algorithms, such as a PID controller, a feed-forward controller and adaptive controllers, are experimentally and numerically validated and compared. It is proven that adaptive controllers enable nanometric precision positioning, but in point-to-point positioning applications can give rise to large overshoots and issues related to lengthy settling times. It is shown that these problems can be minimized by employing the Koopman-based model predictive control that allows simplifying the modeling burden while successfully compensating the frictional effects.